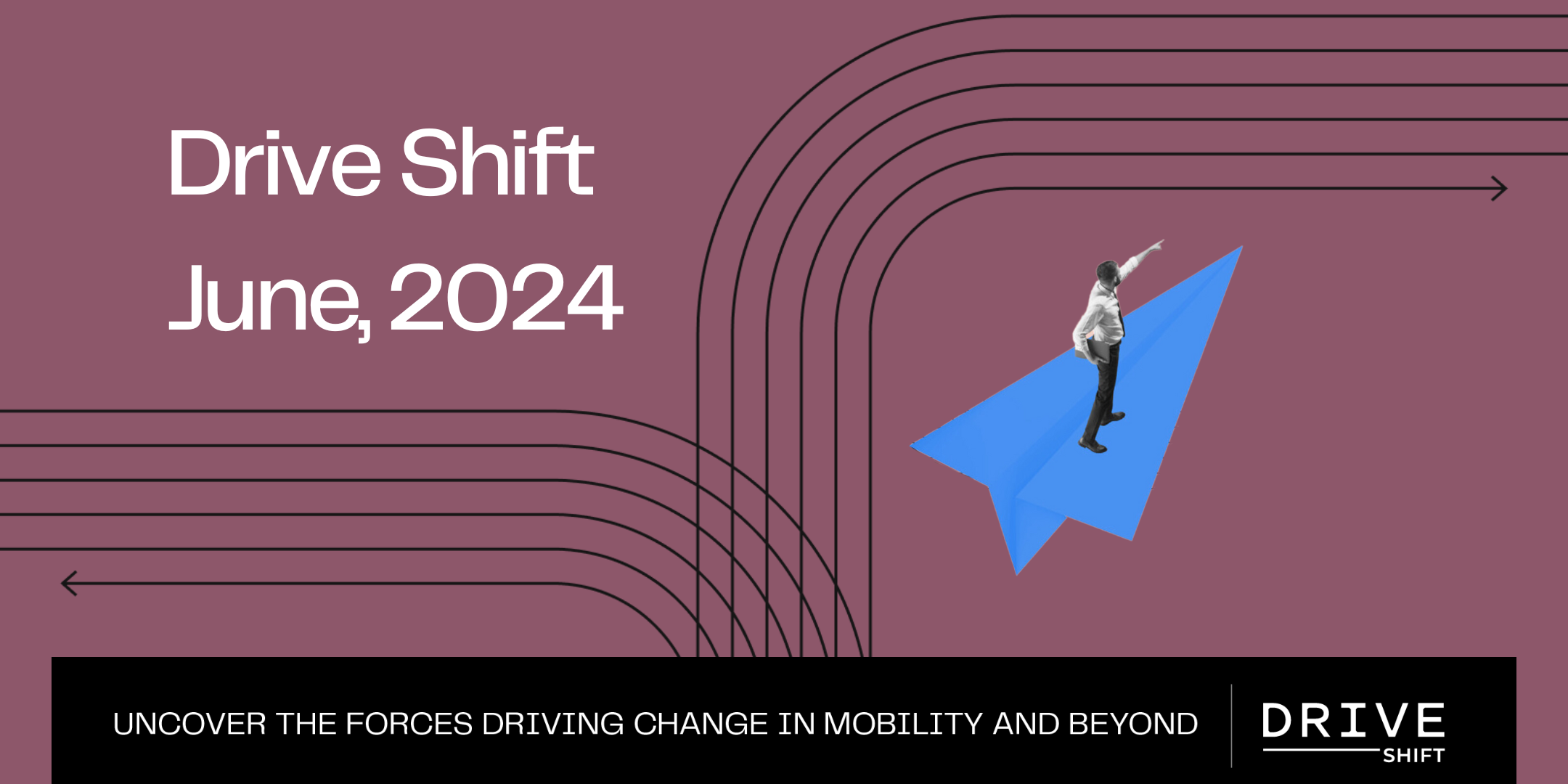
As the demand for electric vehicles continues to surge, the quest for more efficient, sustainable, and cost-effective battery solutions intensifies. While battery innovation tries to tackle diverse aspects, from the manufacturing process and structural changes to weight reduction and chemical composition alterations, Sodium batteries have emerged as an intriguing development, recently gaining momentum.
Sodium-ion batteries operate on the same fundamental principles as lithium-ion batteries: ions move between the anode and cathode through an electrolyte. The key difference lies in the use of sodium (Na) instead of lithium (Li) as the charge carrier. This seemingly small change has significant implications.
So, how can sodium batteries be better than lithium batteries? Firstly, sodium is over 500 times more abundant than lithium, as we can find it in seawater, salty lakes and mineral spring water, making it more accessible and cheaper to collect and use as production material. Furthermore, the fact that sodium batteries can use aluminum for the anode current collector instead of copper, which is used in lithium-ion batteries, further reduces costs. Additionally, sodium-ion batteries have a higher operating temperature range, which makes them potentially safer as they are less prone to overheating and thermal runaway, thereby reducing the risk of fires. And finally, the environmental impact of sourcing sodium is generally lower than that of lithium, making sodium-ion batteries a more sustainable option.
Given these advantages, the EV industry is beginning to explore the potential of sodium batteries. Despite the well-known dominance of the Chinese ecosystem in the global battery industry, China continues to play a significant role also in the development of alternatives, including sodium batteries. For example, earlier this year, BYD, a global leader in EVs and batteries, launched its first sodium-ion battery plant. Additionally, the Volkswagen-backed Yiewi EV brand from JAC Group started delivering a new sodium-ion battery-based EV in recent months.
The development of sodium batteries is not confined to China. Companies worldwide are joining the race to perfect this technology. For instance, the Swedish company Northvolt launched a sodium-ion battery with an energy density of 160 Wh/kg, while Stellantis Ventures invested in France-based Tiamat, focusing on commercializing sodium-ion battery technology. Startups like Peak Energy, Bedrock Materials, and Unigrid have each raised around $10 million to accelerate their sodium battery development.
However, before crowning sodium batteries as the new standard for EV batteries, it's important to acknowledge that mass adoption is still a distant goal. Currently, sodium batteries are at a much less developed stage than lithium batteries, resulting in higher production costs. Additionally, there are technical challenges that need to be addressed as sodium batteries currently have lower energy density (meaning less energy per unit of weight or volume) and shorter lifespan compared to lithium batteries. Therefore, significant innovation is still required to overcome these hurdles, and the companies we mentioned, along with others, are striving to find the solutions.
Every year, billions of tires worldwide reach the end of their life cycle. Traditional disposal methods, such as landfilling or incineration, not only cause visual pollution but also pose significant environmental and health risks. Even while in use, tires release an estimated 6 million tonnes of wear particles globally each year, a problem that will only worsen as the heavier weight of electric vehicles increases tire friction with the road, exacerbating tire wear. In response to these concerning figures, which have raised concerns among the public and regulators, the automotive and tire industry has been actively seeking solutions in recent years to significantly reduce the environmental impact throughout the entire life cycle of tires.
First, the industry is trying to deal with the materials and methods in which the tires are made. Eco-friendly tires are designed with sustainability at their core. Traditional tires are made from a combination of natural and synthetic rubbers, which have a significant environmental footprint. Eco-friendly tires, however, use materials like silica, plant-derived oil, biomass-derived rubber and recycled materials. These materials not only reduce reliance on non-renewable resources but also improve fuel efficiency by reducing rolling resistance. In the past year, nearly all leading tire industry companies, including Bridgestone, Continental, and Pirelli, have announced the launch of new eco-friendly tire series. These tires will be composed of more than 50% renewable rubber and "green" materials, with the future goal of maximizing the use of these sustainable materials and reducing the reliance on conventional rubber.
In addition, a lot of effort is invested in tracking and monitoring the condition of the tire. Tire monitoring and sensing technologies can significantly reduce negative environmental impacts by enhancing tire performance and longevity. Real-time data on tire pressure, temperature, and tread wear enables drivers to maintain optimal tire conditions and prevent premature tire failures, extending the lifespan of tires and reducing the frequency of replacements. By optimizing tire usage and minimizing waste, these technologies contribute to a more sustainable and environmentally friendly transportation system. While Tire Pressure Monitoring Systems (TPMS) have been familiar for many years, recent times have seen advancements in this field as tire sensors have become more sophisticated. A prime example is the sensor technology developed by Enervibe, a Drive TLV’s FastLane company, which uses its energy harvesting solution and tire sensors to provide real time comprehensive information about the tire.
And finally, recycling solutions have experienced significant growth, driven by major tire companies and innovative startups developing technologies to transform end-of-life tires from hazardous waste into valuable raw materials within the circular economy. For instance, Circtec, a UK-based company, raised €150 million last month to establish a tire pyrolysis recycling (process of thermal decomposition of materials) facility. Through Circtec's advanced process, end-of-life tires can be repurposed into recycled materials for the rubber and plastics industries, as well as sustainable drop-in fuels. This exemplifies the concept of a circular economy, where resources are reused and regenerated, demonstrating a sustainable approach to waste management.
In conclusion, tire innovation is not just about improving performance, but it's about driving towards a sustainable future. By embracing these advancements, we can ensure that the tires of tomorrow are smarter, greener, and more efficient, paving the way for a cleaner world.
Urban areas worldwide are becoming increasingly congested as populations grow and cities expand. This densification brings several challenges. Navigating crowded streets and finding parking spaces are daily struggles for many city dwellers, contributing to stress and inefficiency. In addition, the environmental impact of numerous large vehicles operating in close quarters is significant, exacerbating air quality issues and accelerating climate change.On our last visit to Amsterdam for our partners week, we were exposed to what could be the efficient solution to these problems - microcars.
Microcars, also known as city cars or mini cars, offer a practical solution to these urban challenges. These compact vehicles measure under 2.5 meters in length and 1.5 meters in width, typically designed for speeds of up to 90 km/h (though much lower speeds are usually sufficient for city driving), and seat one to two passengers. Their small size allows them to be highly maneuverable, enabling easier navigation through crowded streets and quicker parking in tight spaces, making them ideal for dense urban environments. Additionally, almost all microcars available today are electric, further reducing their environmental footprint and helping to mitigate urban air pollution. Furthermore, unlike regular EVs, microcars have a much lower weight, which significantly reduces non-exhaust emissions.
Today, the automotive industry is increasingly recognizing the potential of microcars, with both established OEMs and innovative newcomers entering the market. Traditional automakers like Citroen, with its Ami model that has sold 50,000 vehicles in the past four years and was recently launched in a new version, as well as Opel with the Rocks-e, and Renault with its former Twizy and current Mobilize Duo, have acknowledged the demand for compact, efficient urban vehicles. These companies continue to refine their models to meet modern needs, demonstrating a commitment to this growing market. Simultaneously, new entrants such as Microlino, Biro and Silence as well as the Israeli City Transformer are pushing the boundaries of microcar design. With most microcars priced below $20,000, entering the EV market through these vehicles presents an intriguing strategy for automotive companies.
However, microcars face challenges that could hinder widespread adoption. Safety concerns are significant, as their small size makes them more vulnerable in collisions. Additionally, their limited speed, range, and seating capacity may not suit all potential customers. Urban infrastructure must also adapt to support the growing number of electric microcars, requiring more charging stations and dedicated parking spaces.
Without underestimating the importance of these issues, it appears that microcars have the potential to play a significant role in the future urban mobility mix. A survey conducted by McKinsey found that about 35% of consumers would consider replacing their current vehicle with a microcar, while 55% would consider using these vehicles for specific trips. When these numbers are combined with the growing market demand and the active involvement of OEMs and startups, it becomes clear that microcars have a promising future.
As the demand for electric vehicles continues to surge, the quest for more efficient, sustainable, and cost-effective battery solutions intensifies. While battery innovation tries to tackle diverse aspects, from the manufacturing process and structural changes to weight reduction and chemical composition alterations, Sodium batteries have emerged as an intriguing development, recently gaining momentum.
Sodium-ion batteries operate on the same fundamental principles as lithium-ion batteries: ions move between the anode and cathode through an electrolyte. The key difference lies in the use of sodium (Na) instead of lithium (Li) as the charge carrier. This seemingly small change has significant implications.
So, how can sodium batteries be better than lithium batteries? Firstly, sodium is over 500 times more abundant than lithium, as we can find it in seawater, salty lakes and mineral spring water, making it more accessible and cheaper to collect and use as production material. Furthermore, the fact that sodium batteries can use aluminum for the anode current collector instead of copper, which is used in lithium-ion batteries, further reduces costs. Additionally, sodium-ion batteries have a higher operating temperature range, which makes them potentially safer as they are less prone to overheating and thermal runaway, thereby reducing the risk of fires. And finally, the environmental impact of sourcing sodium is generally lower than that of lithium, making sodium-ion batteries a more sustainable option.
Given these advantages, the EV industry is beginning to explore the potential of sodium batteries. Despite the well-known dominance of the Chinese ecosystem in the global battery industry, China continues to play a significant role also in the development of alternatives, including sodium batteries. For example, earlier this year, BYD, a global leader in EVs and batteries, launched its first sodium-ion battery plant. Additionally, the Volkswagen-backed Yiewi EV brand from JAC Group started delivering a new sodium-ion battery-based EV in recent months.
The development of sodium batteries is not confined to China. Companies worldwide are joining the race to perfect this technology. For instance, the Swedish company Northvolt launched a sodium-ion battery with an energy density of 160 Wh/kg, while Stellantis Ventures invested in France-based Tiamat, focusing on commercializing sodium-ion battery technology. Startups like Peak Energy, Bedrock Materials, and Unigrid have each raised around $10 million to accelerate their sodium battery development.
However, before crowning sodium batteries as the new standard for EV batteries, it's important to acknowledge that mass adoption is still a distant goal. Currently, sodium batteries are at a much less developed stage than lithium batteries, resulting in higher production costs. Additionally, there are technical challenges that need to be addressed as sodium batteries currently have lower energy density (meaning less energy per unit of weight or volume) and shorter lifespan compared to lithium batteries. Therefore, significant innovation is still required to overcome these hurdles, and the companies we mentioned, along with others, are striving to find the solutions.
Every year, billions of tires worldwide reach the end of their life cycle. Traditional disposal methods, such as landfilling or incineration, not only cause visual pollution but also pose significant environmental and health risks. Even while in use, tires release an estimated 6 million tonnes of wear particles globally each year, a problem that will only worsen as the heavier weight of electric vehicles increases tire friction with the road, exacerbating tire wear. In response to these concerning figures, which have raised concerns among the public and regulators, the automotive and tire industry has been actively seeking solutions in recent years to significantly reduce the environmental impact throughout the entire life cycle of tires.
First, the industry is trying to deal with the materials and methods in which the tires are made. Eco-friendly tires are designed with sustainability at their core. Traditional tires are made from a combination of natural and synthetic rubbers, which have a significant environmental footprint. Eco-friendly tires, however, use materials like silica, plant-derived oil, biomass-derived rubber and recycled materials. These materials not only reduce reliance on non-renewable resources but also improve fuel efficiency by reducing rolling resistance. In the past year, nearly all leading tire industry companies, including Bridgestone, Continental, and Pirelli, have announced the launch of new eco-friendly tire series. These tires will be composed of more than 50% renewable rubber and "green" materials, with the future goal of maximizing the use of these sustainable materials and reducing the reliance on conventional rubber.
In addition, a lot of effort is invested in tracking and monitoring the condition of the tire. Tire monitoring and sensing technologies can significantly reduce negative environmental impacts by enhancing tire performance and longevity. Real-time data on tire pressure, temperature, and tread wear enables drivers to maintain optimal tire conditions and prevent premature tire failures, extending the lifespan of tires and reducing the frequency of replacements. By optimizing tire usage and minimizing waste, these technologies contribute to a more sustainable and environmentally friendly transportation system. While Tire Pressure Monitoring Systems (TPMS) have been familiar for many years, recent times have seen advancements in this field as tire sensors have become more sophisticated. A prime example is the sensor technology developed by Enervibe, a Drive TLV’s FastLane company, which uses its energy harvesting solution and tire sensors to provide real time comprehensive information about the tire.
And finally, recycling solutions have experienced significant growth, driven by major tire companies and innovative startups developing technologies to transform end-of-life tires from hazardous waste into valuable raw materials within the circular economy. For instance, Circtec, a UK-based company, raised €150 million last month to establish a tire pyrolysis recycling (process of thermal decomposition of materials) facility. Through Circtec's advanced process, end-of-life tires can be repurposed into recycled materials for the rubber and plastics industries, as well as sustainable drop-in fuels. This exemplifies the concept of a circular economy, where resources are reused and regenerated, demonstrating a sustainable approach to waste management.
In conclusion, tire innovation is not just about improving performance, but it's about driving towards a sustainable future. By embracing these advancements, we can ensure that the tires of tomorrow are smarter, greener, and more efficient, paving the way for a cleaner world.
Urban areas worldwide are becoming increasingly congested as populations grow and cities expand. This densification brings several challenges. Navigating crowded streets and finding parking spaces are daily struggles for many city dwellers, contributing to stress and inefficiency. In addition, the environmental impact of numerous large vehicles operating in close quarters is significant, exacerbating air quality issues and accelerating climate change.On our last visit to Amsterdam for our partners week, we were exposed to what could be the efficient solution to these problems - microcars.
Microcars, also known as city cars or mini cars, offer a practical solution to these urban challenges. These compact vehicles measure under 2.5 meters in length and 1.5 meters in width, typically designed for speeds of up to 90 km/h (though much lower speeds are usually sufficient for city driving), and seat one to two passengers. Their small size allows them to be highly maneuverable, enabling easier navigation through crowded streets and quicker parking in tight spaces, making them ideal for dense urban environments. Additionally, almost all microcars available today are electric, further reducing their environmental footprint and helping to mitigate urban air pollution. Furthermore, unlike regular EVs, microcars have a much lower weight, which significantly reduces non-exhaust emissions.
Today, the automotive industry is increasingly recognizing the potential of microcars, with both established OEMs and innovative newcomers entering the market. Traditional automakers like Citroen, with its Ami model that has sold 50,000 vehicles in the past four years and was recently launched in a new version, as well as Opel with the Rocks-e, and Renault with its former Twizy and current Mobilize Duo, have acknowledged the demand for compact, efficient urban vehicles. These companies continue to refine their models to meet modern needs, demonstrating a commitment to this growing market. Simultaneously, new entrants such as Microlino, Biro and Silence as well as the Israeli City Transformer are pushing the boundaries of microcar design. With most microcars priced below $20,000, entering the EV market through these vehicles presents an intriguing strategy for automotive companies.
However, microcars face challenges that could hinder widespread adoption. Safety concerns are significant, as their small size makes them more vulnerable in collisions. Additionally, their limited speed, range, and seating capacity may not suit all potential customers. Urban infrastructure must also adapt to support the growing number of electric microcars, requiring more charging stations and dedicated parking spaces.
Without underestimating the importance of these issues, it appears that microcars have the potential to play a significant role in the future urban mobility mix. A survey conducted by McKinsey found that about 35% of consumers would consider replacing their current vehicle with a microcar, while 55% would consider using these vehicles for specific trips. When these numbers are combined with the growing market demand and the active involvement of OEMs and startups, it becomes clear that microcars have a promising future.